Companies have to organize, plan, and keep track of maintenance actions to achieve top-quality performance. Planning and scheduling for maintenance are two different tasks used in conjunction to develop the maintenance plan. As it sounds, maintenance planning is the process of planning, while maintenance scheduling is the process of reconfiguring workloads in a manufacturing process. Maintenance scheduling helps assign machinery and plant resources and plan human resources. Design manufacturing processes and purchase material.
Computerized Maintenance Management Systems (CMMS) give you the tools to schedule and plan maintenance, track the things you value and then act upon the outcomes. But, a successful implementation process is crucial to maximizing the power of a system for managing maintenance.
Maintenance Plan
Maintenance planning is usually described as a comprehensive process that pinpoints possible problems before time and provides strategies for addressing the issues. For instance, maintenance planning lists the tools and resources needed for the task. It also makes sure they’re readily available and laid out where required. The role of a planner is to establish the procedure to finish a job. The handling of parts, the ordering process stage, management breakdown management, and quality control are some of the primary issues to consider in the maintenance plan.
Scheduling
The planning phase is the one that determines the tasks that need to be completed; the scheduling phase concerns when work is to be completed and who is to be assigned the task. To maximize your maintenance processes, ensure that you schedule the highest amount of work or preventive maintenance tasks that could be completed with your available resources.
It is recommended to schedule your work in accordance with the essential work requests. If you don’t have the internal resources to plan, schedule, and carry out a maintenance program, seek out a maintenance service with the expertise required for industrial maintenance.
Having The Right CMMS Implementation Team
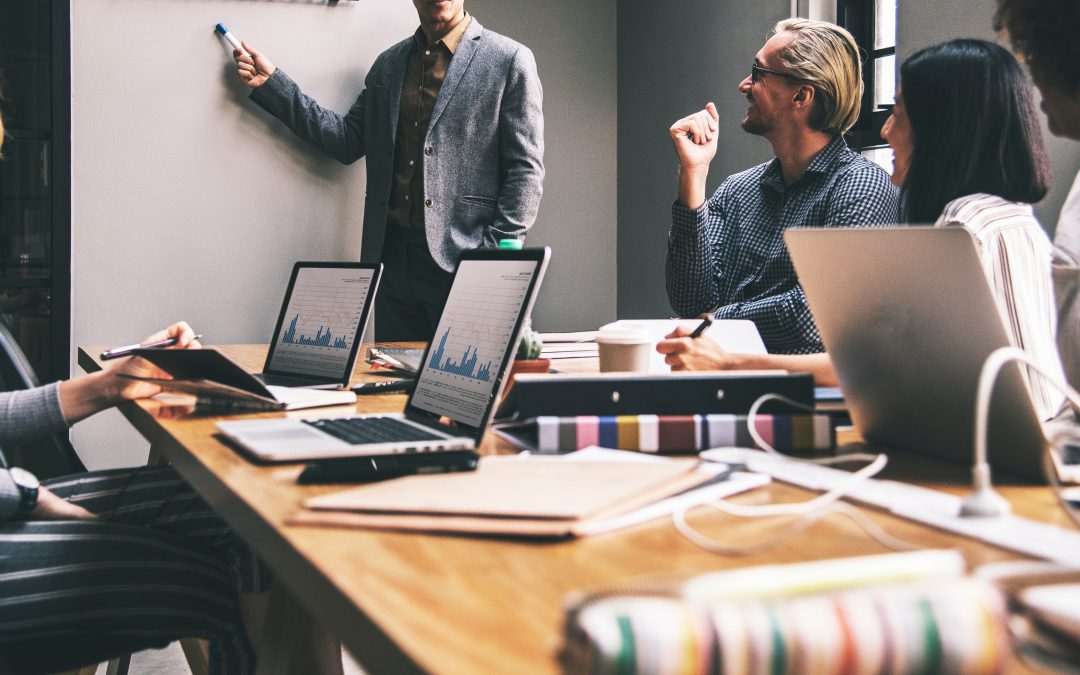
Source: faciliworks.com
Setting up the CMMS implementation team will help you achieve the success of installing software. Choose your team from an array of cross-functional members from within your team. The team members could be from many departments, including maintenance and IT materials management, maintenance, and many more.
The maintenance planner has an essential role in fulfilling. Maintenance planners are responsible for managing your backlog of work and resources in line with maintenance tasks to be completed. The maintenance planner can also develop practical and innovative methods to determine and achieve goals.
In addition, the proper CMMS will help to reduce idle time. The idle time meaning is simply the time that an asset is in usage yet isn’t productive. It’s not the same as downtime; that is when your assets aren’t productive due to scheduled maintenance or an unexpected issue. It’s impossible to eliminate idle time; however, you can take steps to cut it down.
Start by examining how you arrange your workspaces and equipment, focusing on ergonomics and cycle time. The maintenance department should be set up with cutting-edge CMMS software to help reduce idle time. Since there’s a clear correlation between idle times and time spent in downtime, implementing a PM program can help increase productivity and profit.
The Benefits of Maintenance Planning and Scheduling
Reduced Maintenance Costs
The planned maintenance program offers a fantastic opportunity to lower maintenance expenses. By laying out a preventive maintenance program, minor issues and repairs that are simple can be identified before they develop into major problems and expensive repairs.
Extended Asset Life
Regularly servicing equipment extends the life span of assets. Inspecting and maintaining equipment and keeping it running in good shape can extend the time it is in operation, which means it doesn’t have to be replaced every so often.
Increased Workplace Safety
Making sure that equipment is not damaged is in everyone’s best interest. Not only do you benefit from the savings in cost discussed earlier, however, but employees and others who work who are close to the equipment are also safe with a reduced risk of accidents.
Improved Workplace Culture
Planning maintenance can reduce not only downtime for equipment but also employee downtime. Planned maintenance is preventive, and easing the strain of unexpected equipment malfunctions keeps employees engaged, working together, and overall more content.
Planned Maintenance Decreases Downtime
If an asset is left unprotected, it is likely to fail. Failures, faults, and breaks can disrupt entire production processes, leading to many hours, if not even days, of downtime that is not planned. This is costly, particularly when you consider that operations and labor costs continue to rise while productivity has slowed.
Regular maintenance schedules allow minor problems to be dealt with before they become major malfunctions. The process of collecting data and prioritizing maintenance tasks make sure that the most urgent issues are dealt with first, thereby keeping critical assets from getting damaged further. The planning process ensures all the required materials and equipment are readily available. In the end, the planned downtime is reduced to a minimum as work is done within the scheduled time.
Maintenance Planning and Scheduling Tips
Make Sure You Have a Quality Maintenance Plan
As was briefly mentioned earlier, maintenance planner jobs descriptions tend to demand crew technicians who are senior in rank, build rapport with colleagues, and understand the plants well. They must be proficient and possess a good understanding of the principles and practices of maintenance planning.
Train The Planner Properly.
Ensure that the maintenance planners know how to utilize your work order software at your plant, which includes the pulling of reports and data, to ensure they can comprehend the history of maintenance on equipment.
Give Feedback On Tasks Completed.
Up-to-date, accurate data is crucial to creating effective maintenance plans. Just declaring “complete” or “fixed” does not provide sufficient information that can help determine what’s working and what’s not. When technicians have completed a task, they must provide thorough feedback – either positive or negative – on the planner using the software that manages work orders.
Changes According to Feedback.
Technicians give feedback to their colleagues to provide a reason. Planners must examine all feedback to ensure that work orders are enhanced or still efficient. It also shows the technicians that their voice is acknowledged, which helps them provide positive feedback.
Final Words
Use these maintenance scheduling and planning strategies to cut costs, increase the reliability of equipment and improve the effectiveness and efficiency of your maintenance operations. A well-planned maintenance plan and schedule will help your business become better competitors in the global market.